Why should you get your laser alignment tool calibrated? Why should you get it repaired, if needed?
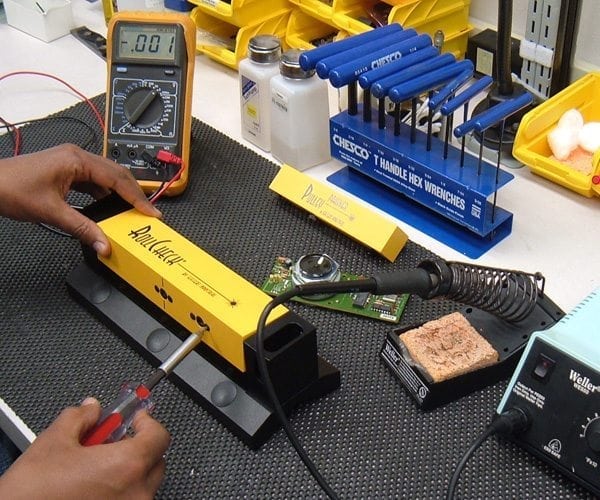
Precision
Measurements matter, don’t they? You want measuring tools to give you the correct information each and every time you use them. If they don’t, that could cost a lot of time and money, not to mention headaches!
Routine Checkups
Laser alignment tools are like people– sometimes they need a “check-up” to see how they’re doing. Ideally, if a measurement is “off,” then machinery can fail and shutdowns are imminent. Product quality can also be negatively affected. Meanwhile, people could get injured. And then there’s the time it takes to complete maintenance work caused by the tool that wasn’t accurate– yikes!
Ideally, laser alignment tools should be calibrated at least once every other year. For those working with high-precision and ISO standards, once a year calibrations make sense.
All Encompassing
Calibrations and/or repairs take into account a number of things. Serial numbers get checked so that system parts correspond as intended. There’s a correct charger/function check with the system. Also, there’s a correct license check to ensure all new functions are available. Software in display and measurement units get updated. How’s the laser power? Does it need adjustment? How are the detectors doing? A communication check between devices can be performed. In general, an overall system check can be done so measurements are taken, saved, and a report created– basically, a “check-up” to make sure everything’s working well.
Calibrations may take about a week and costs vary based on the system. Why get calibrations and repairs done? Well, you don’t want the costs associated with a production stoppage, do you? And you don’t want to deliver improperly manufactured products! So, laser tool alignment calibration and repair is a smart investment that pays off.
For more info, contact Seiffert Industrial today.